Myers Industries Reveals Q2 Financials
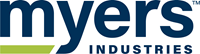
Myers Industries Inc., a manufacturer of polymer and metal products and distributor for tire, wheel and under-vehicle service industry, announced results for the second quarter ended June 30.
Q2 2024 Financial Highlights:
- Net sales of $220.2 million compared with $208.5 million in the prior-year period
- Net Income of $10.3 million, compared with $10.6 million in the prior-year period
- Adjusted EBITDA of $38.9 million, compared with $24.7 million in the prior-year period
- GAAP gross margin of 34.3%, up 150 basis points versus the prior-year period
- Adjusted gross margin of 36.1%, up 320 basis points versus the prior-year period
- GAAP net income per diluted share of $0.28 compared with $0.29 in the prior-year period
- Adjusted earnings per diluted share of $0.39 compared with $0.35 in the prior-year period
- Cash flow provided by operations of $14.3 million and free cash flow of $9.9 million
Myers Industries President and CEO Mike McGaugh said, “Our second-quarter results reflect the company’s first full quarter with Signature Systems. This business is benefiting from worldwide investments in Infrastructure and helped drive both sequential and year-over-year revenue growth and margin expansion. Signature’s performance outpaced the demand headwinds in the Recreational Vehicle (RV), Marine and Automotive Aftermarket end markets.”
“We continue to focus on growing our Storage, Handling & Protection portfolio, most notably our four power brands: Akro-Mils, Buckhorn, Scepter, and Signature Systems. We believe our increased participation in the Military and Infrastructure end markets will provide meaningful growth for our Company over the next several years.
At the same time, we are taking actions to reduce costs and increase productivity in the Engineered Solutions and Automotive Aftermarket portfolios. These actions include the consolidation of three distribution centers in our Myers Tire Supply business, as well as today’s announcement of the consolidation of our Atlantic, Iowa, rotational molding facility into our other rotational molding plants in Indiana. We are able to reduce our footprint and reduce our cost structure, due to the productivity gains we’ve achieved. We expect these closures to be completed in 2025 and deliver approximately $5 million in cost savings in 2025 as well.
Our ongoing productivity-improvement and cost-reduction initiatives will help us navigate the cyclical demand conditions in the RV, Marine, and Automotive Aftermarket end markets while positioning the company favorably for when these conditions revert to historical levels of demand.”