How To Achieve an Accurate Inventory Count Without a Yearly Count
A little extra work up front can prepare your dealership for year-round inventory accuracy — and help avoid the cost and disruption of annual counts.
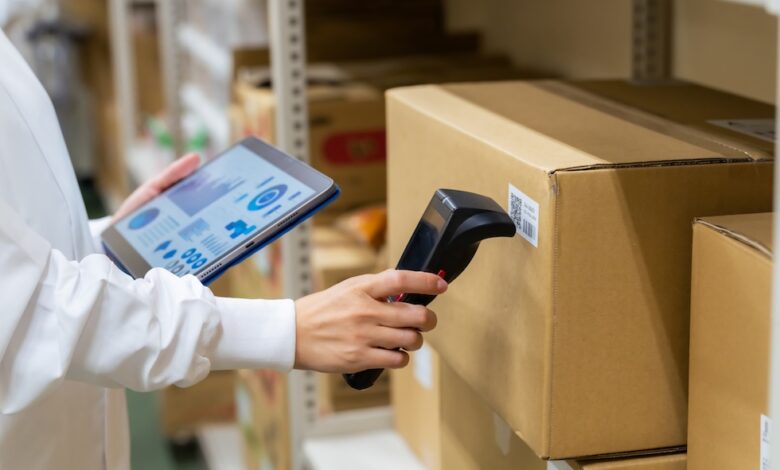
It is July and still a few months before your parts department will be processing the annual counting of the parts and accessories inventories — usually referred to as “the physical.” I thought it appropriate to focus my July column on inventory accuracy and an alternate method of achieving it. So, if you decide to implement my ideas, you have almost six months to prepare.
In the previous millennium (actually 1989), I developed a plan that could increase the accuracy of my actual and reported inventories without having to schedule a yearly “physical” — at least not more than once.
Because I disliked the cost and added workload of a yearly counting of my inventories, and because I wanted my inventories to be accurate each day, I developed a program titled PAIRS (Parts and Accounting Inventory Reconciliation System). I discussed the concept with the dealer principal, and he agreed to allow me to try it for one year at the end of which we (dealer principal, accounting manager and me, the parts manager) would review the results to determine if this would become our policy.
PAIR-ing Accounting & Parts
The PAIRS concept (and PAIRS Manual) is based on continuous counting of segments of the inventories according to frequency and quantity of usage, coupled with monthly reconciliation of the parts department value of the inventories with the accounting department value of the inventories.
Because we would be introducing several new processes related to the PAIRS program, we commenced each of these processes in August of that year. These processes included:
- Identifying items by velocity of movement, which were:
- items sold almost weekly or at least 40 times/year
- items sold monthly or at least 12 times/year
- items sold quarterly or at least four times/year
- all other items with three or fewer sales/year
- Identifying which inventory exceptions would be evaluated and the frequency of these exception reports (e.g., no bin location, minus on-hand and others as appropriate)
- Determining how the cycle counts would be processed based on the four velocity of movement classes
- Developing a process for researching and adjusting inventory discrepancies
- Creating a document/report to inform the accounting department of any count adjustments
- Developing forms for recording each transaction type that impacted the value of the inventory, such as stock receipts, adjustments, returns to suppliers, purchases at more or less than standard replacement cost, acquisition of free items, etc.
- Creating an inventory reconciliation form for monthly comparison of the month-end parts department value to the month-end accounting department value
- Deciding what variance percentage between the two values is acceptable and determining what research each of the departments would do to determine the cause of any percentage value that is greater than the accepted norm
- Any other processes identified during this procedural trial stage
The Three Phases of PAIRS
The PAIRS Manual has more than 100 pages. Only a few processes and policies contained in the PAIRS Manual have been included in this column. If you are interested in the PAIRS concept, please contact me via email.
Phase 1: Preparation
Since it would be necessary to establish an accurate and equivalent base for the accounting department value and the parts department value, a one-time “physical” was scheduled for the period Dec. 26-30, 1989. During this period, the dealership would be closed for all business so that no parts transactions other than those involved with the processing of the “physical” would be transacted. The preparation phase accounts for more than 25 pages in the PAIRS Manual.
Following is a few of the many tasks that are needed in the preparation phase:
- Determine the number of and skills of the personnel required to efficiently and accurately perform the several functions required to process a physical count and verification so that any training needed can be processed before the physical — this includes accounting department personnel and the general manager who should participate in the verification aspects of the physical so they can accept the results.
- Meet with your management team to coordinate the dates for the physical count and clarify that no transactions will be processed during that period.
- Procure the materials and equipment required, which could include handheld scanners, clipboards, pens, ink cartridges, flashlights, step stools and any other items deemed necessary.
- Generate and process any reports of the inventory database (exceptions reports, work-in-process report, count sheets, etc.) so that it is as clean as possible.
Phase 2: Processing
This portion of the PAIRS Manual accounts for more than 20 pages and assumes that two eight-hour days are allotted for the actual processing of the physical counting, verification and completion of the many tasks required to perform an accurate, verified physical.
So that personnel are diligent as they perform the several tasks involved in an accurate, verified physical, I suggest limiting the workdays to eight hours or no more than 10 hours. Lunches should be provided so that none of the personnel need to leave.
Phase 3: Maintenance & Reconciliation
This portion of the physical will be continued on a monthly cycle after the physical has been processed because the tasks involved in this portion will be necessary to maintain the accuracy of the inventory on a perpetual basis.
These routines are the basis of the PAIRS concept because they require the parts and accounting departments to coordinate their functions that impact the values of the parts and accessories inventories.
As needed, the managers and personnel of these two departments should communicate any events that could impact the inventory values so that any discrepancies can be identified and resolved within each month.
Since we started our PAIRS concept in August, we had several months during which each department could establish and perfect the routines necessary to maintain and reconcile our parts and accessories inventories via a monthly cycle.
Is It Worth the Work?
You decide! As with most of my suggestions, it will be necessary to do some work to implement my PAIRS concept. To assist you in deciding whether to proceed, please consider this eventual result: By implementing the PAIRS concept and processes, we were able to achieve an inventory accuracy greater than 99%, and we also eliminated the expenses and labor related to processing an annual physical.
If you are interested in learning more about the PAIRS concept, please contact me.
Click here for more business advice from Mel Selway.