Working Away from Wood: Composites Find Footing in RV Flooring
Composite FRP flooring – in place of plywood – may just be the new big thing in product improvement in the towables segment.
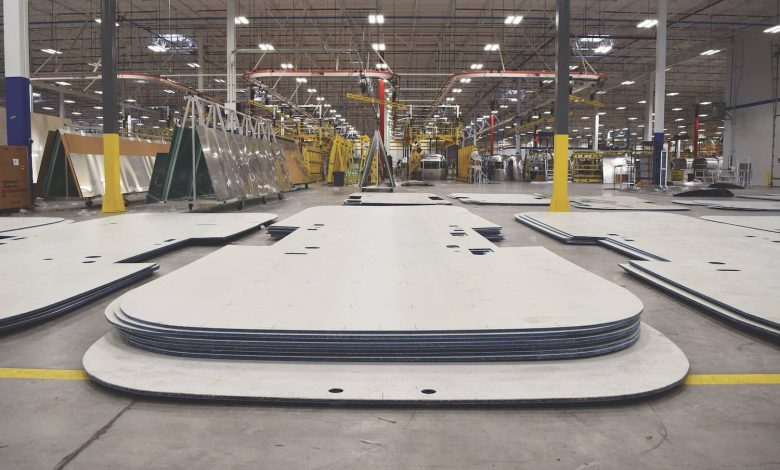
When it comes to a new RV model upgrade, its common to think of updates related to creature comforts, exterior and interior styling enhancements and new floorplans – the cosmetics of the thing. When it comes to the “bones” of that unit, the excitement is typically less pronounced.
Still, there’s a new idea for a truly basic part of any RV – the floor – that’s making an early showing in the marketplace and which will likely have designers and manufacturers thinking some new thoughts in the months and years to come.
While that space above the chassis-and-insulation and below the carpet or LVT (luxury vinyl tile) has traditionally been reserved for a wood overlay, composite materials are the new next thing. And those who use or sell them say they offer some distinct advantages to Mother Nature’s finest.
A Product for Innovators
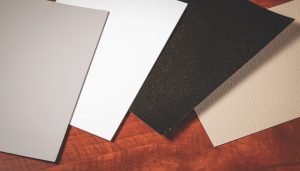
For supplier Polser International, fiberglass-reinforced plastic products (FRP) and composite fiber-reinforced plastic materials are a way of life. For Airstream, the desire was to get the last bits of wood out of the company’s iconic silver bullet aluminum trailers.
Regardless of where they’re coming from, both companies believe composites are an excellent option for the middle of that RV-floor sandwich – and for the same reasons.
Look up a definition for “composite material” on the internet, and sources will say it’s a combination of two materials with different physical and chemical properties. When glued or bonded, they create a material to do a particular job, for instance, become stronger, lighter, or even resistant to electricity. They can also improve strength and stiffness.
For Jackson Center, Ohio-based Airstream, the move to a composite material for the 2021 model year of its Airstream line comes as the company moved into a new production facility early this year. However, Dana Gehman, an engineer who worked on finding the right composite for the RVs, says that more than anything, the move was about the continuous improvement of Airstream’s products.
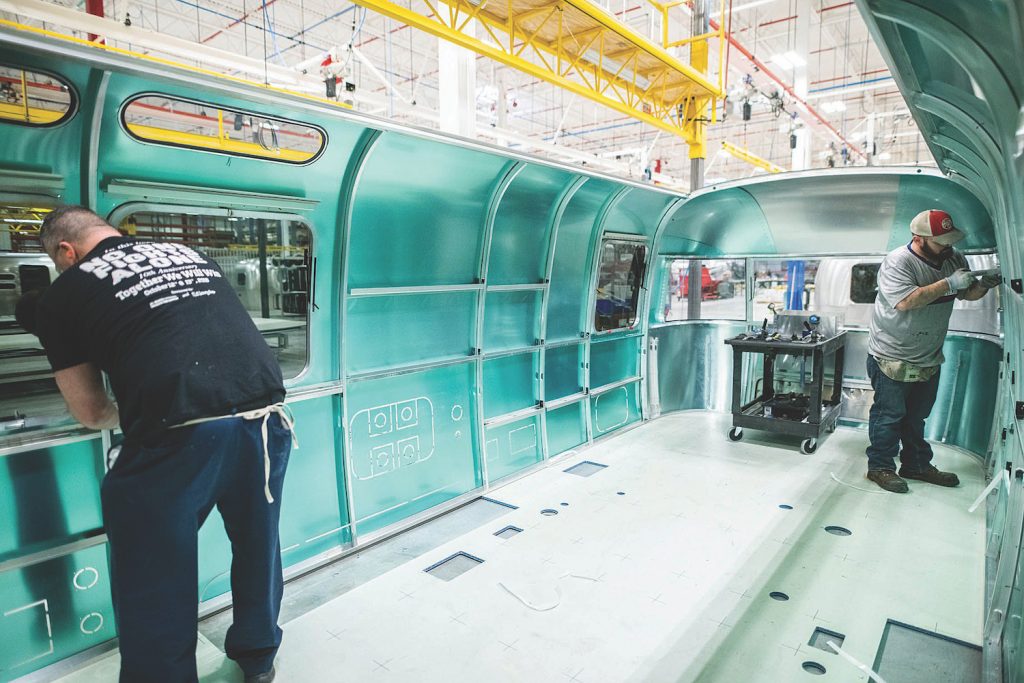
“Obviously, the plywood floors on the many, many Airstreams out there have performed extremely well for many, many years,” Gehman says. “Many Airstreams out there have the original plywood floors in them. But we’re always seeking something better – and composite floors give us the opportunity to remove the last piece of wood as a primary part of our structure. We saw that as something that would benefit the future of Airstream going forward.”
He compares it to residential homebuilding, where wood has also given way to a host of more efficient materials.
Greg Glanders, president of Elkhart, Ind.-based Polser USA, also is anxious to spread the word that composites are a new option for RV flooring. Polser USA is a limited liability corporation spun off from Turkish-based Polser International earlier this year.
So far, Polser’s biggest splash came at the end of July, when it was announced the company had reached an exclusive partnership agreement with Winnebago Industries to provide a permanent anti-microbial coating on the interior walls of its Class A motorhomes.
However, Glanders’ background is in composite materials, and he says several OEMs are testing the company’s composite flooring as a first step in bringing that product to the market.
“These are products for people who want to be the innovators, who want to be the leaders,” Glanders says. “This is something they can talk about with their customers. This is something to upsell.”
Reducing the Squeaks
So, just what are proponents of composite materials saying to sell their flooring? The main message is simple: It’s not wood.
*With the introduction of composite flooring, no more wood inside Airstream trailers. For Airstream, taking that last bit of wood out of its units means if there’s ever a leak somewhere, there aren’t going to be any issues with the flooring, according to McKay Featherstone, vice president of product development.
Polser’s Glanders elaborates, noting that wood can create a lot of warranty issues for the OEMs, or an extra repair expense for the owners of older units no longer covered.
“The nature of the RV is that you cut holes in the floor so you can connect your various water tanks and other utilities,” he says. “If there’s a leak somehow, some way, and the wood gets wet, it swells. And, when it swells, it also rots, and you can have mold and mildew.”
Featherstone uses the word “inorganic” to describe Airstream’s new flooring. He notes that wood floors can create other issues as well, right down to the fact that they sometimes squeak.
“We now have an aluminum shell that has no organic material in it,” he says.
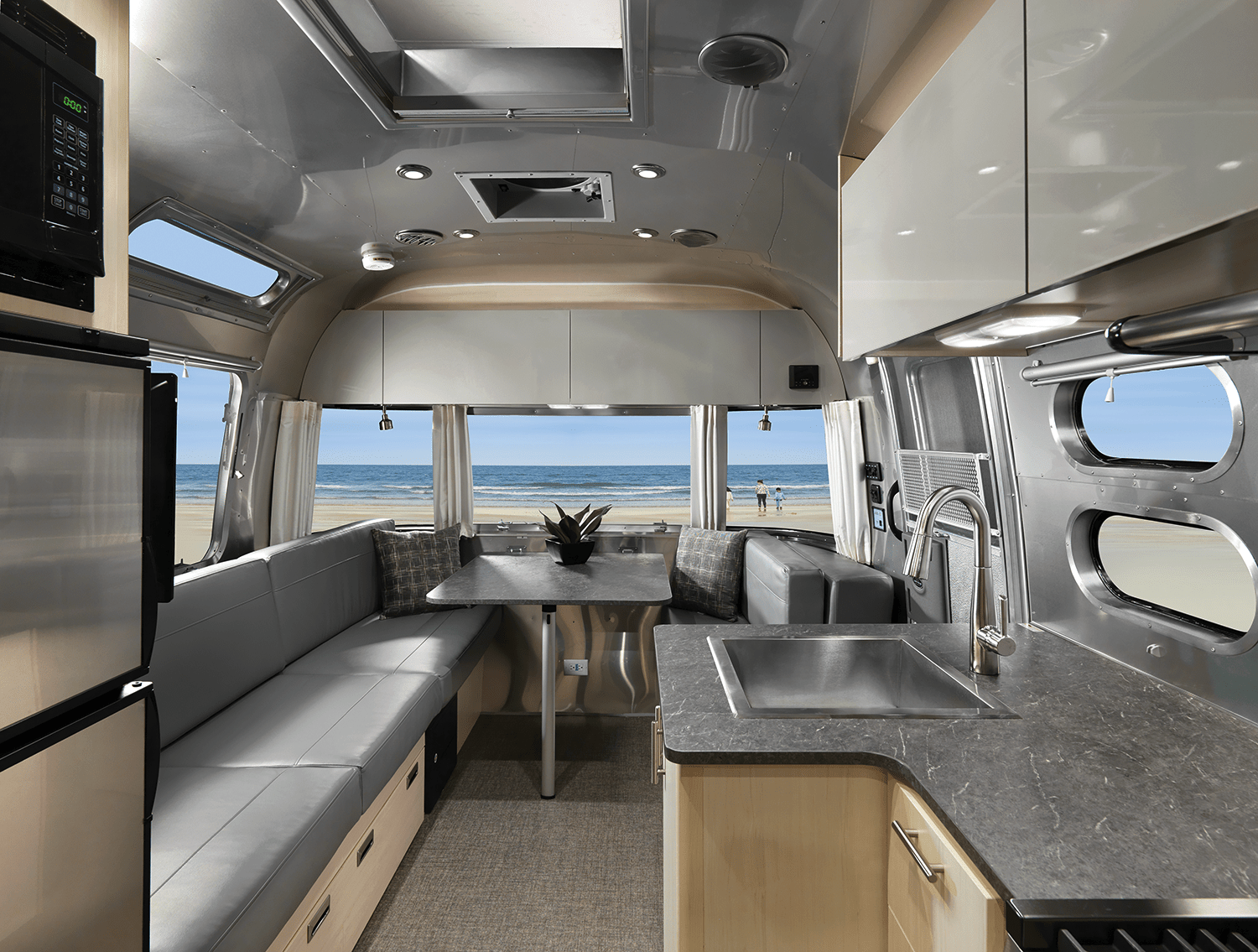
Still, there must be other advantages beyond reducing the squeaks – and there are. One is weight. The products are uniformly referred to as “lightweight composites,” although just how much lighter depends on the composite and the wood it’s replacing.
“Anytime we can take weight out while improving other things is always great,” says Featherstone.
However, in these cases, it’s light enough – and flexible enough – to be installed in one piece. Glanders notes that these composites are often sold in a coil. “If you’re an OEM, you’re buying this in whatever your width requirement is,” he says. “Say it’s 96 inches wide. You’re working with a 96-inch-wide coil, and it can be cut to whatever length is needed. Not only is it efficient, but there are no seams.”
Featherstone agrees that, not only is the stiffness of the composite Airstream uses attractive but it, too, felt drawn to the idea of being able to install it as a single sheet. At Airstream, that also gives it another advantage.
“Because it’s one large floor, we can print on the top of that floor the location information for our associates,” says Featherstone. “If there’s a screw that needs to go down, if there’s a part that needs to be in the exact right place, we can print on the composite and that’s going to help our associates be more accurate and more repeatable with the assembly.”
Yet another advantage: These products have good screw retention.
“People know that wood has good screw retention,” says Polser’s Glanders. “But our material has a very high level of fiberglass in the resin, and the higher the content of fiberglass, the better it is for the screw to grasp the fiberglass strands in the product.”
Constant Improvement
The fact that Polser’s product has a very high level of resin also points out an important part of the lightweight composite story. The product can be created and adapted to meet each OEM’s needs.
From Glanders’ perspective, that’s a real advantage his company brings to the table. “We really listen to our customers, and if somebody wants a 2-mm or 2.5-mm or even 3-mm product, we can do exactly what the customer wants,” he says. “We have the ability to fine-tune and tweak things so that we can hit that magic mark between performance and price – and both those things are very important.”
When Glanders’ hiring was announced, he stated he planned to work closely with potential clients and their engineers to develop products that offer the best and most-innovative solutions for their specific needs.
Coming at it from the OEM perspective, Airstream’s Gehman says that company didn’t reinvent the wheel in finding its composite. Instead, it went out and evaluated numerous existing composite materials already in the marketplace.
“We also looked at what are emerging products, because there’s so much going on constantly within the composites field,” Gehman says. “We found a company that was quite local here to us in Ohio that was developing emerging technologies. The product we’re using has been in a parallel marketplace, and we worked with them to develop it for our use.”
The parallel industry: transportation, and more specifically tractor trailers, refrigerated vans and cargo trailers – all with applications where a light weight and protection from moisture also are important.
Possibly the one area where composites can’t be said to offer much improvement is in the area of insulation. Airstream’s Gehman says it compares well to wood because there is a foam layer involved in the flooring construction, but more generally it’s the construction of the entire unit that’s going to cut down on cold floors.
Glanders says Polser’s product “does have an R-value associated to it,” that stems mainly from its density. He estimates it’s about an R-6.
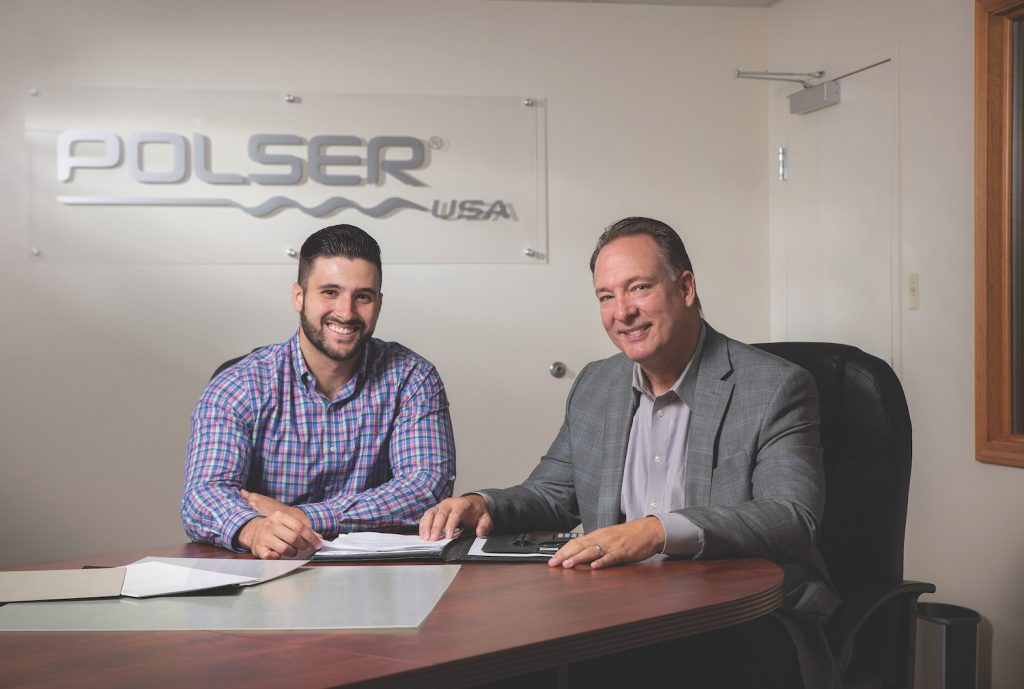
It’s still early in the game, but will wood eventually be chased from RV floor construction across the board? Probably not. For now, it’s continuing in Airstream’s motorhomes and the company’s popular Basecamp model.
“The motorhomes are different,” Featherstone says. “It’s just a completely different structure. It’s more about technical reasons.”
However, he adds the RV maker will undoubtedly continue to study the matter as it seeks to improve its products.
Glanders feels wood will continue to be used – at least in some units – because of its lower price.
“If you’re building the cheapest units out there, you’ll have wood,” he says. “But other people are going to want to be leaders and innovators. They’re going to invest in composites and then they’re going to use them to upsell.”