RV News
10 Tips for Business Owners Impacted by a Pandemic
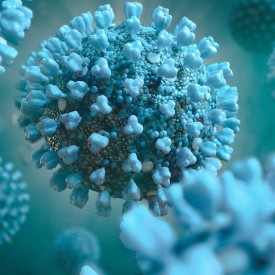
COVID-19 has brought business almost to a halt, and we are still in shock about how quickly life has changed. Rather than watching the news all day, we can take the opportunity to use the time to catch up with some chores that may have fallen behind. Here is a brief list of things we can quickly focus on, which will improve our business in the long run and perhaps improve our dispositions.
- Clean up the showroom and workspace. Disinfect all counters, doors, and other places people touch.
- Throw out all those things that have accumulated and you swore you would use someday (that someday is long past).
- See what maintenance and repairs are needed on equipment.
- That dreaded filing… it’s time to catch up.
- It may be time to archive your accounting system.
- Clean up your website; post new images, new products and deals, check all your text for spelling and relevancy, and check all links.
- You may even have time to paint a wall or two, or clean carpets, without disturbing customers.
- Catch up on your social media postings. If you post, be positive.
- If you are open for business, use social media and your website to let people know.
- Reach out to customers who may be in need to see if you can help.