Lippert’s Plant 50 Earns VPP Merit Certification
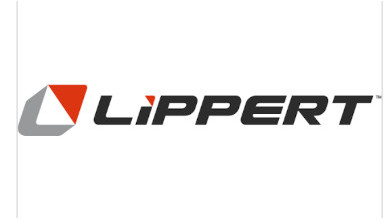
Lippert has partnered with the Indiana Department of Occupational Health and Safety (IOSHA) and its Voluntary Protection Program (VPP) and has announced that its Plant 50 has been recognized with Merit Certification through 2022.
The VPP is a partnership with IOSHA to promote effective health and safety programs in manufacturing and other industries. Recognition as a VPP Merit Site is referred to as “a testament to sustained excellence in all areas of your safety and health management system,” according to the company.
Plant 50, which produces furniture and mattresses for the RV industry along with mattresses for college dorms and over-the-road trucks, has pursued and secured this partnership to help ensure a comprehensive safety management system is in place, Lippert said.
“The plant has demonstrated, with all 500-plus team members, that their efforts towards team member engagement, management commitment to a safe working environment, hazard control and prevention, and employee training programs are truly world-class,” the company added.
In order to maintain VPP certification and status as a Merit Site, Plant 50 must submit annual safety and health management system evaluations to IOSHA. Management commitment to the program is essential, and conscious efforts to preserve a safe and healthy work environment is required by all – making maintaining the certification a collective process.
“I’m very proud of Plant 50 for the collaborative work they’ve done to make this happen,” said Ryan Smith, group president of North America. “At Plant 50 and Lippert as a whole, we constantly strive to be a team that prioritizes creating and maintaining safe, productive, and synergetic work environments while concurrently improving health and safety performances and programs for the betterment of everyone involved.”
While the certification proclaims Lippert as a world-class facility regarding safety, Lippert said VPP is also of great benefit to its team members as it helps increase employee involvement and engagement; reduces injuries through improved hazard recognition, prevention, and control; and improves employee training, which enhances overall quality. Team members are also equipped with guidelines and a number of employee involvement opportunities so they can do their part and become personally involved in the program.