NTP-STAG’s New Facility Increases Efficiency and Cost-Saving
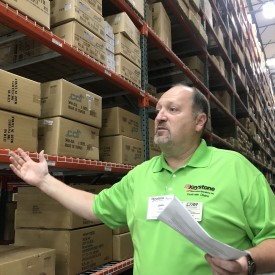
EASTVALE, Calif. – As of July 1, Eastvale, Calif., marks the location of Keystone Automotive/NTP-STAG’s second largest facility/seventh distribution center. The new 450,000-square-foot NTP-STAG distribution center encompasses efficiency. Built under stringent California codes, not only is the building sustainable and safe, but it’s a proof that design influence from world-leading companies like Amazon can inspire speedier practices in the RV industry.
Ground pickers are wire-guided for safety, working two aisles a day, specific to the zone they’re gathering product from. In the small parts area, all lights are on motion sensors as people go through the aisles collecting everything from sparkplugs to nuts and bolts. All told, about 150 people work over the course of three shifts, fulfilling 93,000 orders a day.
Scroll down for more photos of the new facility.
“This was design-built,” John Grier, operational manager of LKQ, said at the grand opening of the facility last week. “We visited different facilities, whether it was Granger, Amazon, or other distribution centers.”
Every design element was made with the intention of reducing distribution time. “In our old facility, we worked out of seven cross-dock doors,” he said. Now there’s 20 doors for shipping, 20 for receiving. “We can pretty much take any trailer that comes at any time. Right now, we’re receiving about $750,000 a day inbound, and about $3 million a week into the property.”
That’s about $18.5 million per month.
The facility – an upgrade from its nearby, smaller Corona, Calif., location it moved from – benefits from several hearty specs. First, there’s 40 rows of aisles and bays with 84 bins in each bay. The overall distance that can be travelled down each 400-foot run equates to “seven football fields,” said Grier. Overhead, helicopter-like fans span 18 feet in diameter to keep the facility cool. And every week about 90,000 orders leave the warehouse.
Beyond size, the company has made several improvements to product handling. To alleviate any scratches from hitches, the company developed a new racking system to buffer them from metal-on-metal contact. “They don’t come with any kind of wrapping from the factory,” said Grier. “So, this is our way to make the merchandise a little better for the customers.”
Against a wall near offices is a row of lockers containing employee scanners for barcode inventorying. Grier references the movie Full Metal Jacket – how each rifle got their own name – the idea being that when a scanner is personalized, employees tend to take better care of it.
Tweaks like this have allowed Keystone Automotive/NTP-STAG to grow to 500 trucks, 800 drivers, and a total of 30 million miles traveled.
In relocating to a larger facility to Eastvale, NTP-STAG execs avoid what’s known locally as the “Corona Crawl” – highway traffic that can add over half an hour to inbound and outbound trucks. Now NTP-STAG’s facility has dedicated dockers and gains more than an hour every day. After six months of operation, the company will learn how much cost-savings there’s been, predicting at least six figures.
“Most of the customers that are served on this fleet have cutoffs that are 5:30 p.m. or later for next-day delivery, so the hour-and-a-half that you picked up by the improvements that we made here,” said John Spaulding, director of communications and events. “Now (customers) can work clear through the end of their day and still order parts, which is huge.
“The idea of the building was to provide a broader deeper service to the customers,” Spaulding continued. “If we could break even on the cost, even better. But we’re able to reach further and later with more product than ever before; and that’s going to open up the different side of the equation with how we service our customer on the sales side.”
This week, the Eastvale location is experimenting with the warehouse loading the trucks at night to gain an additional 45 minutes.
“When you’re in Southern California, that’s important. It means we get to the customer sooner. Customers always want to wait ’til the last minute to order their product, and want it first thing tomorrow morning,” said Grier. “It’s a now world. This helps us fit that marketplace.”